Compliance with the Federal Motor Carrier Safety Administration (FMCSA) regulations is essential for ensuring road safety and meeting legal requirements. The FMCSA enforces rules designed to reduce crashes, injuries, and fatalities involving large trucks and buses. Adhering to these regulations is not optional; it is a mandatory responsibility for all commercial vehicle operators to keep their fleets legally operational and safe.
The FMCSA plays a vital role in establishing and enforcing standards to ensure safe commercial vehicle operations. This federal agency oversees critical aspects of road safety, including driver qualifications, vehicle maintenance, and operational protocols. Its mission is to monitor and enhance safety measures for all commercial drivers across the nation, preventing road accidents and maintaining public trust in the transportation sector.
FMCSA Compliance Checklist
An FMCSA compliance checklist serves as a vital tool for commercial vehicle operators, guiding them through the necessary regulatory requirements to maintain safety and legal standards. By ensuring these standards are met, operators can prevent fines, penalties, and safety breaches that could jeopardize their operations.
Driver Qualification Files: Ensuring Compliance Through Proper Documentation
Maintaining up-to-date and accurate Driver Qualification Files (DQFs) is a critical component of FMCSA compliance. These files serve as a comprehensive record of a driver’s credentials, qualifications, and history, ensuring they meet federal standards for operating commercial vehicles. Properly maintained DQFs help employers demonstrate compliance during audits or inspections and contribute to a safer transportation system.
Key Components of Driver Qualification Files
- Commercial Driver’s License (CDL): A valid CDL is a foundational requirement for any commercial driver. The file must include a clear, legible copy of the driver’s CDL, verifying their eligibility to operate the specific type of vehicle assigned to them.
- Medical Certificates: Drivers must undergo regular medical evaluations to confirm they are physically qualified to operate commercial vehicles. These certificates, issued by FMCSA-certified medical examiners, must be current and retained in the driver’s file. Expired or missing certificates can result in non-compliance.
- Records of Violations: Employers are required to document any traffic violations reported by the driver, as well as those discovered through motor vehicle records (MVR) checks. This includes citations for speeding, reckless driving, or any other infractions that could impact the driver’s qualification status.
- Road Test Documents: Road test results confirm a driver’s proficiency in operating commercial vehicles. While FMCSA regulations may allow an equivalent certification from prior employment, employers must retain documentation of the test or verification that the driver has passed an approved evaluation.
Best Practices for Managing Driver Qualification Files
To ensure compliance and reduce administrative errors, companies should implement the following best practices:
- Digital Documentation: Utilize electronic systems to maintain and organize driver files, making it easier to access and update records as needed.
- Regular Audits: Conduct periodic internal audits of DQFs to verify that all required documents are complete, accurate, and up to date.
- Proactive Expiration Tracking: Implement a tracking system to monitor expiration dates for licenses, medical certificates, and other time-sensitive documents, ensuring timely renewals.
- Training and Awareness: Educate drivers and administrative staff about the importance of maintaining accurate and complete qualification files to avoid non-compliance and penalties.
Proper management of Driver Qualification Files is essential not only for meeting FMCSA requirements but also for promoting a culture of safety and accountability within the transportation industry.
Hours of Service (HOS) Logs: Ensuring Compliance and Promoting Road Safety
Hours of Service (HOS) regulations are a critical aspect of FMCSA compliance, designed to prevent driver fatigue and enhance road safety. Maintaining accurate HOS logs is not only a legal requirement but also a key practice for ensuring that drivers operate within safe limits, protecting both the driver and the public.
Key Requirements for HOS Logs
- Accurate Duty Status Recording: Drivers are required to maintain an accurate log of their duty status for each 24-hour period. This includes tracking time spent on various activities such as driving, on-duty but not driving, off-duty, and sleeper berth. Logs must clearly show start and stop times and provide a complete record of the driver’s daily activities.
- Adherence to Maximum Driving Hours: Drivers must comply with the federal limits for driving hours, which vary depending on the type of operation (e.g., property-carrying or passenger-carrying). These limits include:
- 11-hour driving limit for property-carrying drivers after 10 consecutive off-duty hours.
- 14-hour on-duty limit for property-carrying drivers after starting their workday.
- 60/70-hour weekly limit, depending on the workweek schedule (7-day or 8-day).
Additional Considerations for HOS Compliance
- Mandatory Rest Breaks: Drivers must take a 30-minute break after 8 cumulative hours of driving without at least 30 minutes of off-duty or sleeper berth time.
- Sleeper Berth Provisions: Drivers using sleeper berths must ensure their rest periods meet the minimum required durations, allowing them to split their off-duty time appropriately.
- Short-Haul Exemptions: Certain drivers operating within a 150-air-mile radius may qualify for short-haul exemptions, which simplify log requirements but still mandate compliance with on-duty and driving limits.
- Electronic Logging Devices (ELDs): As per FMCSA regulations, most drivers are required to use ELDs to record HOS data automatically. These devices reduce administrative errors, improve accuracy, and make it easier to manage and share HOS logs during inspections.
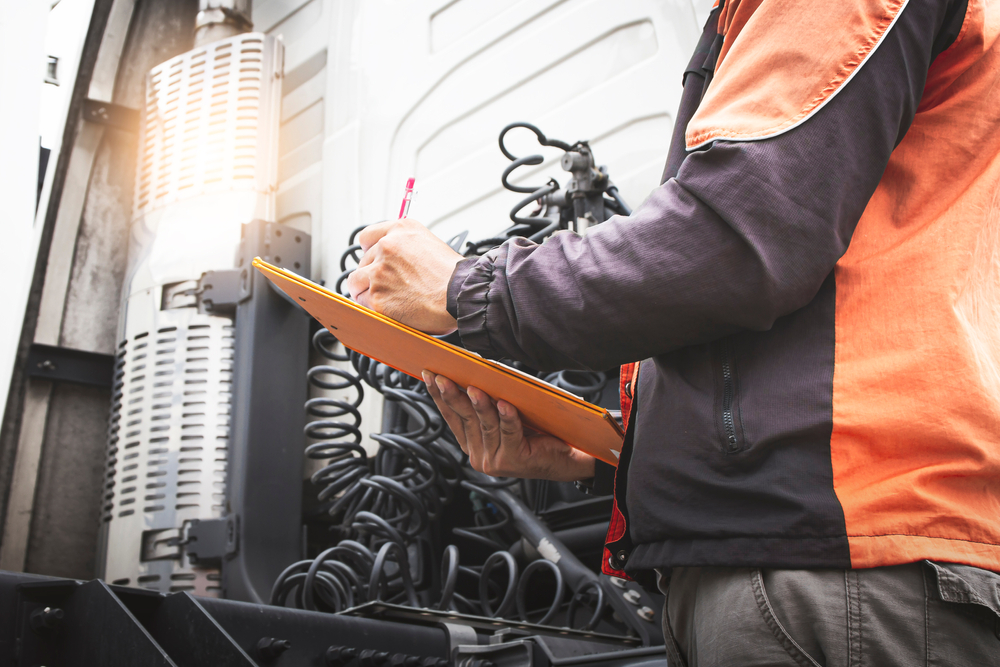
Vehicle Maintenance Records: A Foundation for Compliance and Safety
Vehicle maintenance records are a crucial element of FMCSA compliance, ensuring that all vehicles in a fleet are safe, reliable, and meet federal standards. These records provide a comprehensive history of inspections, repairs, and routine maintenance, serving as evidence of a proactive approach to vehicle safety.
Key Components of Vehicle Maintenance Records
- Inspection Records: Detailed documentation of all pre-trip, post-trip, and periodic inspections is essential. These records should include:
- The date of the inspection.
- The name of the inspector.
- A checklist of inspected components (e.g., brakes, tires, lights, steering systems).
- Notes on any identified defects or maintenance needs.
- Repair Records: Maintenance files must include all repair documentation, such as:
- The nature of the issue or defect.
- Dates of repair.
- Details of the repair work performed.
- The name of the repair technician or service provider.
- Routine Maintenance Logs: Scheduled maintenance activities should be meticulously recorded, including:
- Oil changes, filter replacements, and fluid checks.
- Tire rotations and replacements.
- Brake system maintenance.
- Any manufacturer-recommended services based on mileage or time intervals.
- Parts and Component Replacement Records: Keep track of parts replaced during maintenance or repairs, ensuring compatibility and adherence to FMCSA standards.
Accident Reports: Essential Documentation for Compliance and Safety
Accident reports are a critical component of fleet management and FMCSA compliance. Properly documenting incidents involving commercial vehicles helps ensure regulatory adherence, supports investigations, and provides insights into preventing future accidents. Comprehensive accident reporting is also vital for protecting your company’s legal and operational interests.
Key Elements of a Comprehensive Accident Report
- Date of the Accident: Record the exact date and time the accident occurred. This information establishes a timeline and is essential for regulatory reporting and insurance purposes.
- Location Details: Include precise information about where the accident took place, such as:
- The street address or highway marker.
- The city, state, and zip code.
- Geolocation data, if available, for more accuracy. This helps investigators and stakeholders understand the conditions of the location.
- Injuries or Fatalities: Document any injuries or fatalities resulting from the accident. Be specific and include:
- The number of individuals affected.
- The nature and severity of injuries.
- Whether medical assistance was provided at the scene.
- Vehicle Information: Include details about the commercial vehicle involved, such as:
- Vehicle identification number (VIN).
- License plate number.
- Type and condition of the vehicle.
- Cargo type, if applicable, especially if hazardous materials were involved.
- Driver Information: Record the driver’s details, including:
- Name and contact information.
- Commercial Driver’s License (CDL) number and state of issuance.
- Details of the driver’s condition at the time of the accident (e.g., alertness, signs of fatigue).
- Description of the Incident: Provide a narrative or summary of what occurred, including:
- Sequence of events leading up to the accident.
- Contributing factors such as weather, road conditions, or equipment failure.
- Diagrams or photos of the scene to clarify the events.
- Involvement of Other Parties: Document details about any other vehicles or individuals involved in the accident, including:
- Names and contact information of other drivers.
- Insurance details for all involved parties.
- Descriptions of other vehicles and their license plate numbers.
- Law Enforcement and Emergency Response: Record any law enforcement or emergency services involvement, including:
- Names and badge numbers of responding officers.
- Police report number, if applicable.
- Actions taken at the scene (e.g., citations, towing, arrests).
- Damage Assessment: Include a thorough evaluation of the damage to the vehicle, cargo, and any property affected.
- Witness Statements: If witnesses were present, collect their statements along with their contact information.
Best Practices for Managing Accident Reports
- Immediate Documentation: Drivers should document the accident as soon as it is safe to do so, using standardized forms or electronic reporting tools.
- Photo and Video Evidence: Capture detailed images and videos of the scene, vehicle damage, road conditions, and any relevant signage or signals.
- Training Drivers: Ensure all drivers are trained in accident response protocols, including how to complete reports and collect necessary information.
- Centralized Recordkeeping: Maintain accident reports in a centralized, easily accessible system for audits, insurance claims, and trend analysis.
- Periodic Review and Analysis: Regularly analyze accident reports to identify recurring issues, such as driver behavior, vehicle maintenance problems, or high-risk routes.
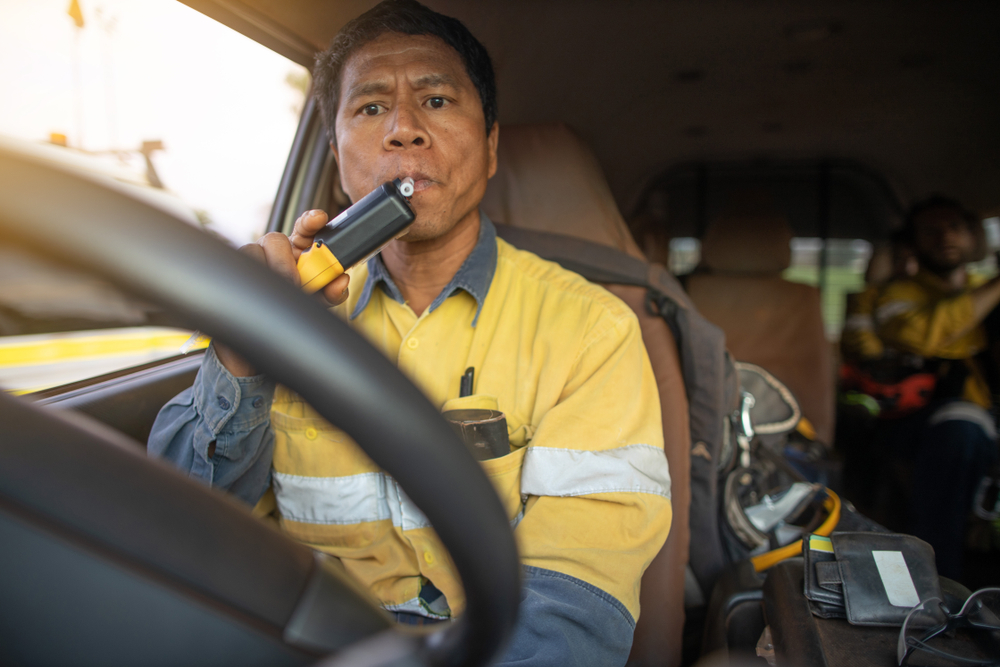
Drug and Alcohol Testing Records: Ensuring Compliance and Workforce Safety
Drug and alcohol testing records are a fundamental part of FMCSA compliance, ensuring that commercial drivers meet safety standards and operate vehicles responsibly. Proper documentation of all required tests provides a clear record of adherence to federal regulations and supports efforts to maintain a safe and compliant fleet.
Key Components of Drug and Alcohol Testing Records
- Pre-Employment Screenings:
- Employers must conduct drug testing for all prospective drivers before they are hired.
- Documentation should include:
- Date of the test.
- Testing results (indicating a pass or fail).
- Name and certification of the testing laboratory.
- Random Testing:
- Random testing is mandated for drivers subject to FMCSA regulations. These tests are conducted throughout the year and must be unannounced.
- Records should include:
- Date and time drivers were selected and tested.
- Documentation showing the random selection process and adherence to federal random testing rates.
- Post-Accident Testing: Following qualifying accidents, drivers involved must undergo drug and alcohol testing. Qualifying accidents are defined as those involving:
- A fatality.
- Bodily injury requiring medical treatment away from the scene, if the driver is cited.
- Disabling damage to any vehicle requiring a tow, if the driver is cited.
- Reports must document:
- Date and time of the test.
- Test results and their relevance to the accident.
- Compliance with FMCSA post-accident testing time frames (e.g., alcohol tests within 8 hours, drug tests within 32 hours).
- Other FMCSA-Mandated Testing Scenarios: Testing is required for specific scenarios, including:
- Reasonable Suspicion Testing: Initiated when a trained supervisor observes behavior or physical signs suggesting drug or alcohol use.
- Return-to-Duty Testing: Required after a driver completes the necessary steps to return to work following a positive test result or refusal to test.
- Follow-Up Testing: Mandated as part of a return-to-duty plan, typically conducted at unannounced intervals.
Hazardous Materials Compliance: Key Requirements for Safety and Adherence
Transporting hazardous materials (hazmat) requires strict compliance with FMCSA and DOT regulations to ensure safety, minimize risks, and prevent incidents. Operators handling hazmat shipments must follow additional training, labeling, and handling protocols to meet federal standards and protect public safety.
Key Components of Hazardous Materials Compliance
- Training Requirements: All employees involved in the transportation of hazardous materials must complete specialized training, including:
- General Awareness Training: Provides an overview of hazmat regulations and the risks associated with transporting hazardous materials.
- Function-Specific Training: Covers the specific responsibilities of employees, such as packaging, labeling, or loading.
- Safety Training: Focuses on emergency response procedures, accident prevention, and proper handling techniques.
- Security Training: Includes measures for preventing unauthorized access to hazardous materials, particularly for high-risk shipments.
- Recurrent Training: Training must be refreshed at least once every three years or whenever regulations change.
- Labeling and Placarding: Proper labeling and placarding are critical to ensure that hazardous materials are correctly identified and handled. Requirements include:
- Displaying appropriate labels on individual packages.
- Using placards on transport vehicles to indicate the class of hazardous materials being carried (e.g., flammable, corrosive, radioactive).
- Ensuring labels and placards comply with size, color, and placement specifications outlined by FMCSA and DOT.
- Shipping Papers: Accurate shipping papers must accompany all hazmat shipments and include:
- Proper shipping name of the material.
- Hazard class and UN/NA identification number.
- Packing group, if applicable.
- Emergency contact information and response procedures.
- A signed certification by the shipper verifying compliance with all applicable regulations.
- Packaging Standards: Hazardous materials must be packaged in containers that meet specific federal guidelines, ensuring durability and resistance to leaks or damage during transit. Key requirements include:
- Using DOT-approved containers for specific materials.
- Marking packages with required information, such as handling instructions or package orientation.
- Handling and Loading Protocols: Hazmat handling requires strict adherence to loading, unloading, and securement procedures, including:
- Preventing the mixing of incompatible materials.
- Securing cargo to prevent movement during transit.
- Inspecting containers for leaks or damage before loading.
- Emergency Response Information: Transporters must carry documentation that outlines emergency response actions for each type of hazardous material being transported. This includes information on:
- Potential hazards.
- First aid measures.
- Procedures for fire, spills, or leaks.
- Hazardous Materials Registration: Companies transporting certain quantities or types of hazardous materials must register with the Pipeline and Hazardous Materials Safety Administration (PHMSA) and pay applicable fees.
FMCSA Compliance Training – Empowering Your Workforce
Ensuring that your workforce is well-versed in FMCSA regulations is essential for fostering a compliant and safe commercial transportation operation. FMCSA compliance training serves not only to educate drivers and fleet operators about current regulations but also to emphasize the importance of integrating safe driving practices into their daily routines.
Regular training is critical for several reasons:
- It keeps staff informed about the latest safety protocols and legislative updates.
- It reinforces the role of safe driving practices and regulatory adherence in daily operations.
- It prepares staff to respond effectively to unexpected situations on the road using proper procedures.
Methods for Delivering FMCSA Compliance Training
A robust FMCSA compliance training program employs diverse methods to ensure thorough and consistent education:
- Onboarding Training: Introduce new hires to compliance protocols from the beginning.
- Periodic Workshops: Provide updates on regulations and company policies to maintain compliance awareness.
- E-Learning Modules: Offer flexible and accessible training for consistent learning opportunities.
- Practical Demonstrations: Incorporate hands-on training to simulate real-world scenarios.
- Regular Assessments: Evaluate understanding and retention, identifying areas that require further focus.
These methods ensure that all employees are well-prepared to comply with FMCSA regulations and contribute to the overall safety and efficiency of your operations.
The Broader Impact of FMCSA Compliance
The importance of FMCSA compliance extends far beyond avoiding fines or penalties. It is integral to fostering a safe, efficient, and reliable transportation industry. Proactive compliance strategies—focused on education, technology, and rigorous monitoring—empower companies to navigate complex regulations while maintaining their commitment to safety and operational excellence.
By embedding compliance into the core of their operations, fleet operators can protect their drivers, ensure public safety, and strengthen their reputation in a highly competitive industry.